ప్రెసిషన్ మెటల్ భాగాలు తరచుగా వివిధ ప్రెసిషన్ మ్యాచింగ్ టెక్నాలజీలను ఉపయోగించి తయారు చేయబడతాయి, CNC మ్యాచింగ్ ఒక సాధారణ పద్ధతి. సాధారణంగా, ప్రెసిషన్ భాగాలు సాధారణంగా కొలతలు మరియు ప్రదర్శన రెండింటికీ అధిక ప్రమాణాలను కోరుతాయి.
అందువల్ల, అల్యూమినియం మరియు రాగి వంటి CNC మ్యాచింగ్ లోహాలను ఉపయోగిస్తున్నప్పుడు, తుది ఉత్పత్తి ఉపరితలంపై సాధన గుర్తులు మరియు గీతలు సంభవించడం ఆందోళన కలిగిస్తుంది. ఈ వ్యాసం లోహ ఉత్పత్తుల మ్యాచింగ్ సమయంలో సాధన గుర్తులు మరియు గీతలకు కారణమయ్యే కారణాలను చర్చిస్తుంది. మేము సంభావ్య పరిష్కారాలను కూడా ప్రతిపాదిస్తాము.
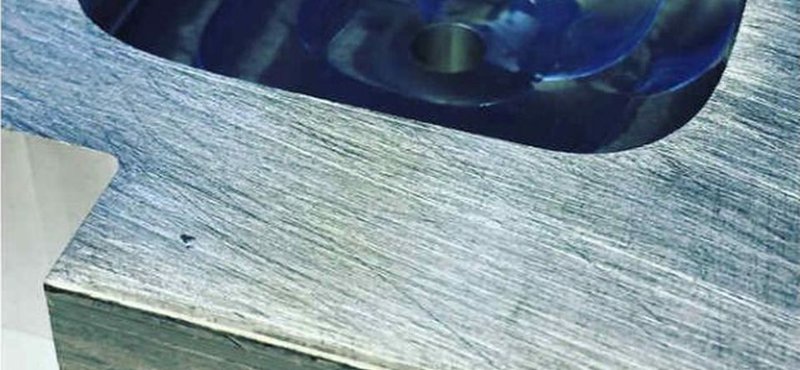
ఫిక్చర్ల బిగింపు శక్తి సరిపోకపోవడం
కారణాలు:కొన్ని కుహరం లోహ ఉత్పత్తులు వాక్యూమ్ ఫిక్చర్లను ఉపయోగించాల్సి ఉంటుంది మరియు ఉపరితల అసమానతల కారణంగా తగినంత చూషణను ఉత్పత్తి చేయడంలో ఇబ్బంది పడవచ్చు, ఫలితంగా సాధన గుర్తులు లేదా గీతలు ఏర్పడతాయి.
పరిష్కారం:దీనిని తగ్గించడానికి, సాధారణ వాక్యూమ్ సక్షన్ నుండి ప్రెజర్ లేదా పార్శ్వ మద్దతుతో కలిపి వాక్యూమ్ సక్షన్కు మారడాన్ని పరిగణించండి. ప్రత్యామ్నాయంగా, నిర్దిష్ట భాగ నిర్మాణాల ఆధారంగా ప్రత్యామ్నాయ ఫిక్చర్ ఎంపికలను అన్వేషించండి, నిర్దిష్ట సమస్యకు పరిష్కారాన్ని రూపొందించండి.
ప్రక్రియ-సంబంధిత కారకాలు
కారణాలు:కొన్ని ఉత్పత్తి తయారీ ప్రక్రియలు ఈ సమస్యకు దోహదం చేస్తాయి. ఉదాహరణకు, టాబ్లెట్ PC వెనుక షెల్స్ వంటి ఉత్పత్తులు సైడ్ హోల్స్ను పంచ్ చేయడం, ఆ తర్వాత అంచులను CNC మిల్లింగ్ చేయడం వంటి మ్యాచింగ్ దశల శ్రేణికి లోనవుతాయి. మిల్లింగ్ సైడ్-హోల్ స్థానాలకు చేరుకున్నప్పుడు ఈ క్రమం గుర్తించదగిన సాధన గుర్తులకు దారితీస్తుంది.
పరిష్కారం:ఎలక్ట్రానిక్ ఉత్పత్తి షెల్స్ కోసం అల్యూమినియం మిశ్రమం ఎంచుకున్నప్పుడు ఈ సమస్యకు ఒక సాధారణ ఉదాహరణ సంభవిస్తుంది. దీనిని పరిష్కరించడానికి, సైడ్ హోల్ పంచింగ్ ప్లస్ మిల్లింగ్ను CNC మిల్లింగ్తో మాత్రమే భర్తీ చేయడం ద్వారా ప్రక్రియను సవరించవచ్చు. అదే సమయంలో, స్థిరమైన సాధన నిశ్చితార్థాన్ని నిర్ధారించడం మరియు మిల్లింగ్ చేసేటప్పుడు అసమాన కట్టింగ్ను తగ్గించడం.
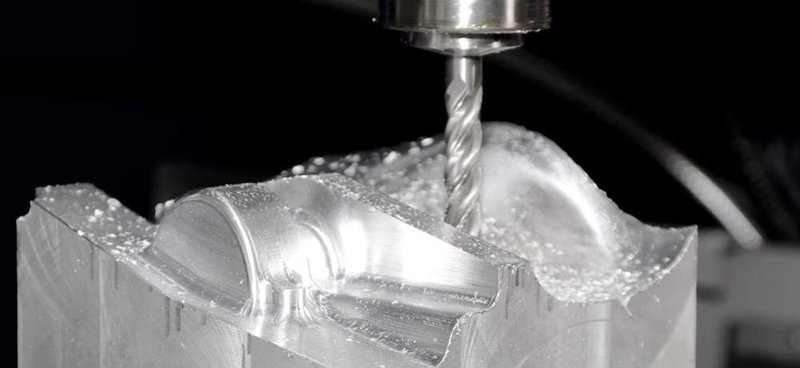
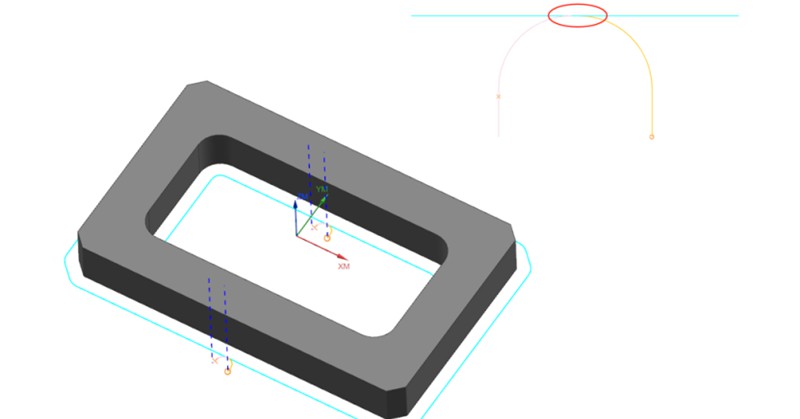
టూల్ పాత్ ఎంగేజ్మెంట్ యొక్క సరిపోని ప్రోగ్రామింగ్
కారణాలు:ఈ సమస్య సాధారణంగా ఉత్పత్తి ఉత్పత్తి యొక్క 2D కాంటూర్ మ్యాచింగ్ దశలో తలెత్తుతుంది. CNC ప్రోగ్రామ్లో పేలవంగా రూపొందించబడిన టూల్ పాత్ ఎంగేజ్మెంట్, టూల్ యొక్క ఎంట్రీ మరియు ఎగ్జిట్ పాయింట్ల వద్ద జాడలను వదిలివేస్తుంది.
పరిష్కారం:ఎంట్రీ మరియు ఎగ్జిట్ పాయింట్ల వద్ద టూల్ మార్కులను నివారించే సవాలును పరిష్కరించడానికి, ఒక సాధారణ విధానంలో టూల్ ఎంగేజ్మెంట్ దూరం (సుమారు 0.2 మిమీ)లో స్వల్ప అతివ్యాప్తిని ప్రవేశపెట్టడం ఉంటుంది. ఈ సాంకేతికత యంత్రం యొక్క లీడ్ స్క్రూ ఖచ్చితత్వంలో సంభావ్య దోషాలను తప్పించుకోవడానికి ఉపయోగపడుతుంది.
ఈ వ్యూహం సాధన గుర్తులు ఏర్పడకుండా సమర్థవంతంగా నిరోధిస్తుంది, అయితే ఉత్పత్తి యొక్క పదార్థం మృదువైన లోహం అయినప్పుడు ఇది పునరావృత యంత్రం యొక్క మూలకాన్ని కలిగిస్తుంది. పర్యవసానంగా, ఈ విభాగం ఇతర ప్రాంతాలతో పోలిస్తే ఆకృతి మరియు రంగులో వైవిధ్యాలను ప్రదర్శించవచ్చు.
ఫ్లాట్ మెషిన్డ్ ఉపరితలాలపై ఫిష్ స్కేల్ నమూనాలు
కారణాలు:ఉత్పత్తి యొక్క చదునైన ఉపరితలాలపై కనిపించే చేప పొలుసు లేదా వృత్తాకార నమూనాలు. అల్యూమినియం/రాగి వంటి మృదువైన లోహాలను ప్రాసెస్ చేయడానికి ఉపయోగించే కట్టింగ్ సాధనాలు సాధారణంగా 3 నుండి 4 ఫ్లూట్లతో కూడిన మిశ్రమ లోహ పదార్థ మిల్లులు. అవి HRC55 నుండి HRC65 వరకు కాఠిన్యాన్ని కలిగి ఉంటాయి. ఈ మిల్లింగ్ కట్టింగ్ సాధనాలు సాధనం యొక్క దిగువ అంచుని ఉపయోగించి నిర్వహించబడతాయి మరియు భాగం ఉపరితలం విలక్షణమైన చేప పొలుసు నమూనాలను అభివృద్ధి చేయవచ్చు, ఇది దాని మొత్తం రూపాన్ని ప్రభావితం చేస్తుంది.
పరిష్కారం:సాధారణంగా అధిక ఫ్లాట్నెస్ అవసరాలు మరియు అంతర్గత నిర్మాణాలను కలిగి ఉన్న ఫ్లాట్ ఉపరితలాలు కలిగిన ఉత్పత్తులలో గమనించవచ్చు. దీనికి పరిష్కారం ఏమిటంటే సింథటిక్ డైమండ్ మెటీరియల్తో తయారు చేసిన కటింగ్ టూల్స్కు మారడం, ఇది సున్నితమైన ఉపరితల ముగింపులను సాధించడంలో సహాయపడుతుంది.
పరికరాల భాగాల వృద్ధాప్యం మరియు అరిగిపోవడం
కారణాలు:ఉత్పత్తి ఉపరితలంపై ఉన్న సాధనాల గుర్తు, పరికరాల కుదురు, బేరింగ్లు మరియు లెడ్ స్క్రూ యొక్క వృద్ధాప్యం మరియు అరిగిపోవడానికి కారణమవుతుంది. అదనంగా, సరిపోని CNC సిస్టమ్ బ్యాక్లాష్ పారామితులు ఉచ్ఛరించబడిన సాధన గుర్తులకు దోహదం చేస్తాయి, ముఖ్యంగా గుండ్రని మూలలను మ్యాచింగ్ చేసేటప్పుడు.
పరిష్కారం:ఈ సమస్యలు పరికరాల సంబంధిత అంశాల నుండి ఉత్పన్నమవుతాయి మరియు లక్ష్య నిర్వహణ మరియు భర్తీ ద్వారా పరిష్కరించబడతాయి.
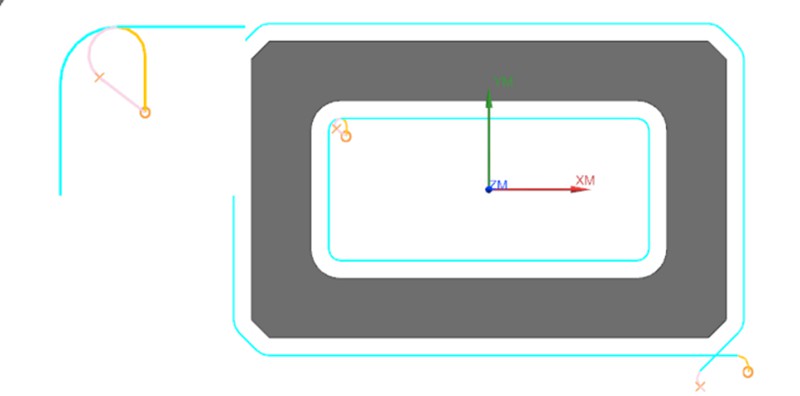
ముగింపు
CNC మ్యాచింగ్ లోహాలలో ఆదర్శవంతమైన ఉపరితలాన్ని సాధించడానికి ఉపయోగకరమైన విధానాలు అవసరం. పరికరాల నిర్వహణ, ఫిక్చర్ మెరుగుదలలు, ప్రక్రియ సర్దుబాట్లు మరియు ప్రోగ్రామింగ్ మెరుగుదలల కలయికతో కూడిన సాధన గుర్తులు మరియు లైన్లను నివారించడానికి వివిధ పద్ధతులు ఉన్నాయి. ఈ అంశాలను అర్థం చేసుకోవడం మరియు సరిదిద్దడం ద్వారా, తయారీదారులు ఖచ్చితమైన భాగాలు డైమెన్షనల్ ప్రమాణాలకు అనుగుణంగా ఉండటమే కాకుండా కావలసిన సౌందర్య లక్షణాలను కూడా ప్రదర్శిస్తాయని నిర్ధారించుకోవచ్చు.